界面新闻实习记者 | 罗容
倒置的塑料瓶被固定在呈螺旋状排列的流水线上,高压水流经由瓶口,正自下而上清洗着塑料瓶内壁。完成这道工序后,塑料瓶被翻转朝上,传送到下一环节等待注入饮料。完成加盖、打码等流程后,一瓶500毫升装的可口可乐就诞生了。
在位于杭州经济技术开发区的浙江太古可口可乐饮料有限公司(下称浙江工厂),一条这样的流水线每秒就能生产出6瓶可口可乐。
“过去两年,太古可口可乐净生产线效率提升超过4%。”9月8日,太古可口可乐(中国)有限公司技术总监骆超向实地探访浙江工厂的界面新闻记者表示。别小看了这个数字,对于一家总计拥有100条生产线的企业来说,意味着可以减少四条生产线的投入。
太古可口可乐是可口可乐公司全球销量第五大的装瓶合作伙伴。该公司旗下的浙江工厂始建于1996年,担负着浙江省大部分地区可口可乐系列产品的生产和销售,年销售额逾30亿元。
提高可口可乐生产线的效率,也同时意味着工厂能耗的降低。减少一条生产线的投入,每年可因此节省500万-800万度电的能源消费。对于浙江工厂而言,这个数字相当可观。
可作为类比的是,该工厂已在屋顶完成了占地2万平方米的光伏板铺设,年发电量可达到60万度。但与节省一条生产线所带来的节能收益相比,仅相当于其十分之一。
而这一切,主要归功于2021年3月部署在浙江工厂的西门子制造信息系统(MIS),该系统由西门子和太古可口可乐联合开发。通过对产线的数字化监控,这套系统能够及时排查出故障设备,减少损失和停机率,并通过能源管理模块,计算出能耗数据,从中找到提升生产线效率的机会点。
浙江工厂工程经理刘继举例称,在部署MIS后,饮料生产过程中的温度数据得以实时抓取。如果发现冷却水的温度已足够低,可以通过控制自动化阀门等措施减少冷却水的流量,从而降低冷却设备的能耗。冷却水的作用,是降低生产过程中可口可乐的温度。利用这一细微调整,浙江工厂生产线平均每年就可节省约10万度电。
MIS目前已部署到太古可口可乐17家工厂的43条产线,由此带来的生产线改进和调整,太古可口可乐全系统的生产能耗在过去两年降低了8%,平均每年节约5000万度电。
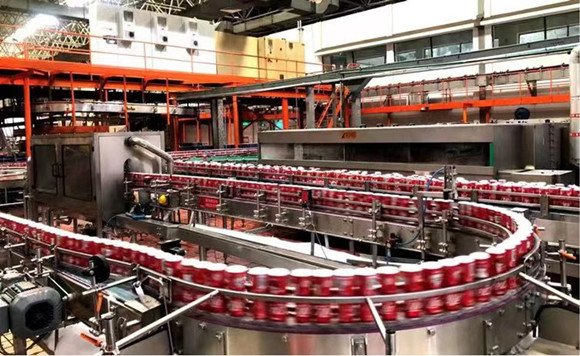
有赖于此,太古可口可乐工厂核心业务的碳排放量与2018年相比降低了24%,预计2030年将进一步降低70%。为此,其已计划今年将MIS系统的应用范围扩大至26家工厂的75条产线。
浙江工厂也并未停下在屋顶铺设光伏的脚步,目前工厂正在进行光伏项目的二期施工,预计装机容量将在现有基础上增长150%。
距离浙江工厂逾175公里的大同齿轮传动(昆山)股份有限公司(下称大同齿轮),同样为降碳目标动起了在屋顶安装光伏的打算。
截至去年底,该工厂屋顶光伏板的覆盖率达到62%,年均发电量200万度,占其总用电量的27%。大同齿轮2000年在当地建厂,主营机加工件产品,其客户名单中就包括西门子。
除了在屋顶铺上光伏板,大同齿轮还于2022年引入了西门子推出的碳足迹可信精算与追溯解决方案(SiGREEN),以实现节能降碳的目标。
SiGREEN的一项重要功能,是计算企业的碳足迹,指导其有效地进行能源效率提升,进而降低碳排放。这套系统的引入,让大同齿轮总经理许正忠有了不少意外发现。
“我们最初跟西门子讨论接入SiGREEN时,考虑的是计算工厂最重要的设备碳排放,并没有打算统计非重点小型设备碳排放,但一些小型设备的能源使用数据让我们吓了一跳。”许正忠告诉界面新闻记者。
根据SiGREEN的统计,大同齿轮厂房顶部所安装的每台巨型节能风扇,一天的用电量为20度,而一台落地风扇的用电量远大于此,通常只供一位工人使用。“有了准确的数据做佐证,我们决定将工厂年内落地风扇数量减少90%。”许正忠称。
现在,厂房顶部不停转动的巨型节能风扇已经替代空调,成为大同齿轮厂区内通风降温的主要途径。在层高11.5米的厂房内,还有三排敞开的天窗,保证车间内的自然采光和空气流通。
大同齿轮此前也曾尝试在厂房内安装空调,但许正忠将其形容为一次失败的经验。“因为空调没有办法把厂区内的热气排出去,造成它根本发挥不了降温的作用。”他解释说。
根据SiGREEN的统计,空调也是大同齿轮夏天耗电量的最大来源。但在空间广阔的厂区内,空调无法把温度降到一定的体感舒适度,并非为工厂降温的高性价比选项。
评论